Schwingtechnik – Effiziente Lösungen mit kontrollierter Vibration
Die Schwingtechnik – auch unter dem Begriff Schwingungstechnik bekannt – ist ein elementarer Bestandteil moderner industrieller Prozesse. Sie beschäftigt sich mit der gezielten Erzeugung, Steuerung und Dämpfung von Vibrationen, um mechanische, elektrische oder pneumatische Prozesse effizienter zu gestalten. In zahlreichen Branchen wie dem Maschinenbau, der Fördertechnik oder der Werkstoffprüfung ist sie aus dem Alltag nicht mehr wegzudenken.
Sie haben noch Fragen?
Die elektromagnetischen Vibrationstische von Aldak halten, was sie versprechen. Sie haben Interesse? Dann melden Sie sich gerne bei uns!
Grundlagen der Schwingungstechnik
Was sind mechanische Schwingungen?
Mechanische Schwingungen sind wiederkehrende Bewegungen eines Körpers um eine Ruheposition. Diese Bewegungen können sowohl gewollt als auch ungewollt auftreten. In der Schwingtechnik wird bewusst mit diesen Bewegungen gearbeitet, um beispielsweise das Verhalten von Komponenten unter Belastung zu testen oder Bewegungsvorgänge zu initiieren – etwa bei Schwingförderern oder Vibrationspressen.
Je nach Frequenz und Intensität wirken sich die Schwingungen unterschiedlich auf technische Systeme aus. Besonders wichtig ist dabei der Einsatz von Schwingungsdämpfern, die auftretende Schwingungsenergien aufnehmen und so Schäden an Maschinen oder Bauteilen vorbeugen. Auch die Effizienz und Präzision von Motoren kann durch gezielte
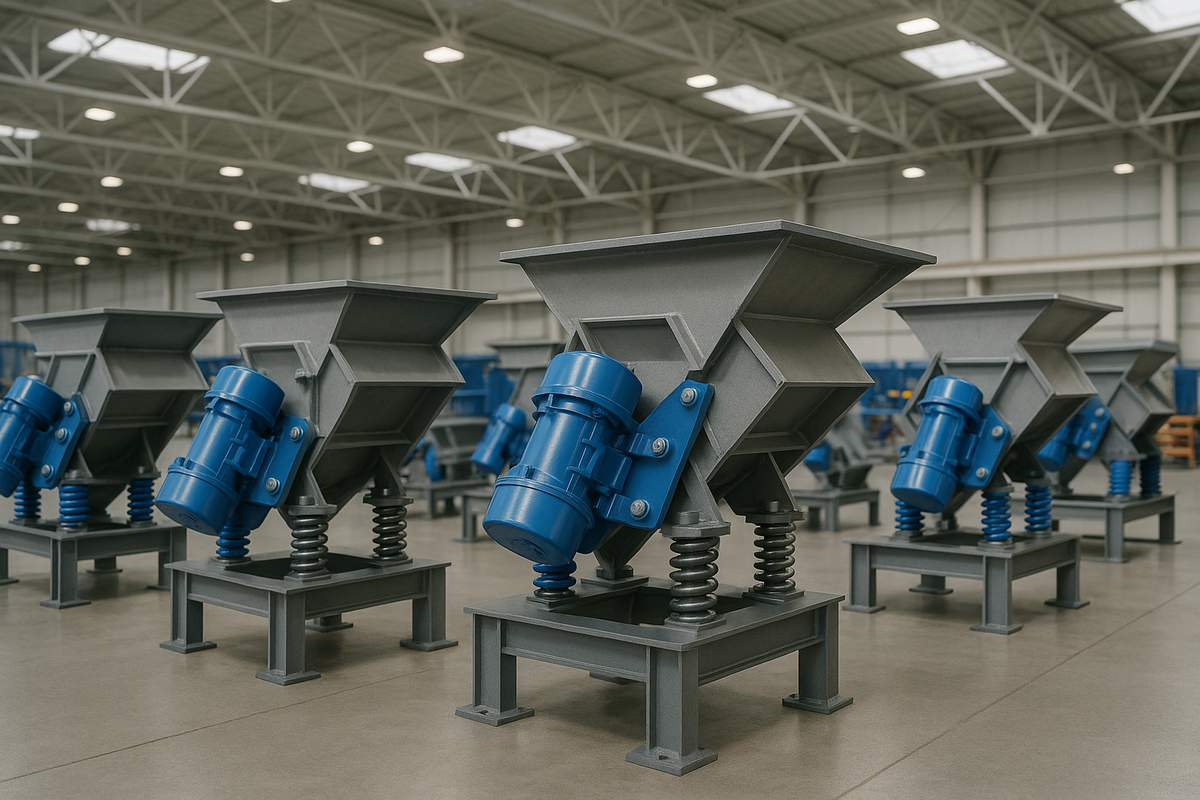
Relevante physikalische Prinzipien
Die Schwingungstechnik basiert auf den physikalischen Grundlagen von harmonischen und unharmonischen Oszillationen. Schwingungen lassen sich mathematisch durch Differentialgleichungen beschreiben, in denen Größen wie Federkonstante, Dämpfungskoeffizient und Masse eine Rolle spielen. Das Ziel der Anwendung ist es, entweder gezielt Vibrationen zu erzeugen oder unerwünschte Schwingungen durch geeignete Maßnahmen zu unterdrücken.
Ein zentraler Begriff ist die Eigenfrequenz: Wird ein System bei dieser Frequenz angeregt, entstehen besonders starke Amplituden – es kommt zur Resonanz. In der Praxis muss dies unbedingt vermieden werden, da es sonst zu irreversiblen Schäden führen kann. Daher wird bei der Entwicklung schwingtechnischer Komponenten großer Wert auf die korrekte Dimensionierung und Abstimmung der Systeme gelegt.
Frequenz, Amplitude und Resonanz
Die Frequenz einer Schwingung – gemessen in Hertz (Hz) – beschreibt die Anzahl der vollständigen Schwingungszyklen pro Sekunde. Die Amplitude gibt die maximale Auslenkung vom Ruhepunkt an und ist ein Maß für die Intensität der Schwingung. Beide Parameter beeinflussen maßgeblich die Wirkung auf technische Systeme.
Tritt eine Vibration mit einer Frequenz auf, die der Eigenfrequenz eines Bauteils entspricht, spricht man von Resonanz. Dies kann zu einer gefährlichen Verstärkung der Schwingung führen, die unter Umständen Lager zerstört, Schraubverbindungen lockert oder ganze Maschinen beschädigt. Daher ist eine sorgfältige Auslegung von Schwingungsdämpfern essenziell, um diese Effekte zu vermeiden und eine zuverlässige Funktion sicherzustellen.
Die gezielte Kontrolle dieser Parameter ist die Grundlage für die Entwicklung effektiver schwingtechnischer Systeme – sei es zur Prozessoptimierung oder zum Schutz vor Schäden durch Vibrationen.
Arten von Schwingungserzeugern
In der Schwingungstechnik gibt es eine Vielzahl an Möglichkeiten, Vibrationen gezielt zu erzeugen. Je nach Anwendung und technischer Umgebung kommen unterschiedliche Arten von Schwingungserzeugern zum Einsatz. Sie bilden das Herzstück vieler Prozesse, in denen Material bewegt, bearbeitet oder geprüft wird. Die Auswahl des richtigen Systems ist entscheidend für die Effizienz, Lebensdauer und Sicherheit der gesamten Anlage.
Mechanische Schwingungserzeuger
Mechanische Schwingungserzeuger arbeiten in der Regel mit rotierenden oder oszillierenden Massen, die durch ihre Bewegung Schwingungen erzeugen. Ein typisches Beispiel ist der Unwuchtmotor: Durch das asymmetrische Gewicht auf der Antriebswelle wird eine permanente Unwucht erzeugt, die die gewünschte Schwingung in die angeschlossene Struktur überträgt.
Diese Systeme sind besonders robust und wartungsarm – ideal für den Einsatz in rauer Industrieumgebung, z. B. bei Förderanlagen, Rütteltischen oder Entleerungshilfen für Silos und Trichter. Sie kommen häufig in Verbindung mit Schwingungsdämpfern zum Einsatz, um eine gleichmäßige und kontrollierte Wirkung auf die Maschine oder das Fördergut zu gewährleisten.
Elektromagnetische Systeme
Für Anwendungen, bei denen eine präzise Regelung der Schwingungsparameter erforderlich ist – etwa in der Messtechnik oder bei empfindlichen Maschinen – eignen sich elektromagnetische Schwingungserzeuger. Sie funktionieren auf Basis eines elektromagnetischen Feldes, das eine Schwingplatte oder einen Anker in Bewegung versetzt. Die Frequenz und Amplitude lassen sich dabei sehr exakt über eine Steuerung regeln.
Elektromagnetische Erzeuger sind besonders leise und verschleißarm. In Kombination mit digitaler Ansteuerung lassen sie sich nahtlos in automatisierte Prozesse integrieren. Ihre feine Regelbarkeit macht sie zur bevorzugten Wahl in Laborumgebungen, bei Werkstoffprüfungen oder in sensiblen Produktionslinien.
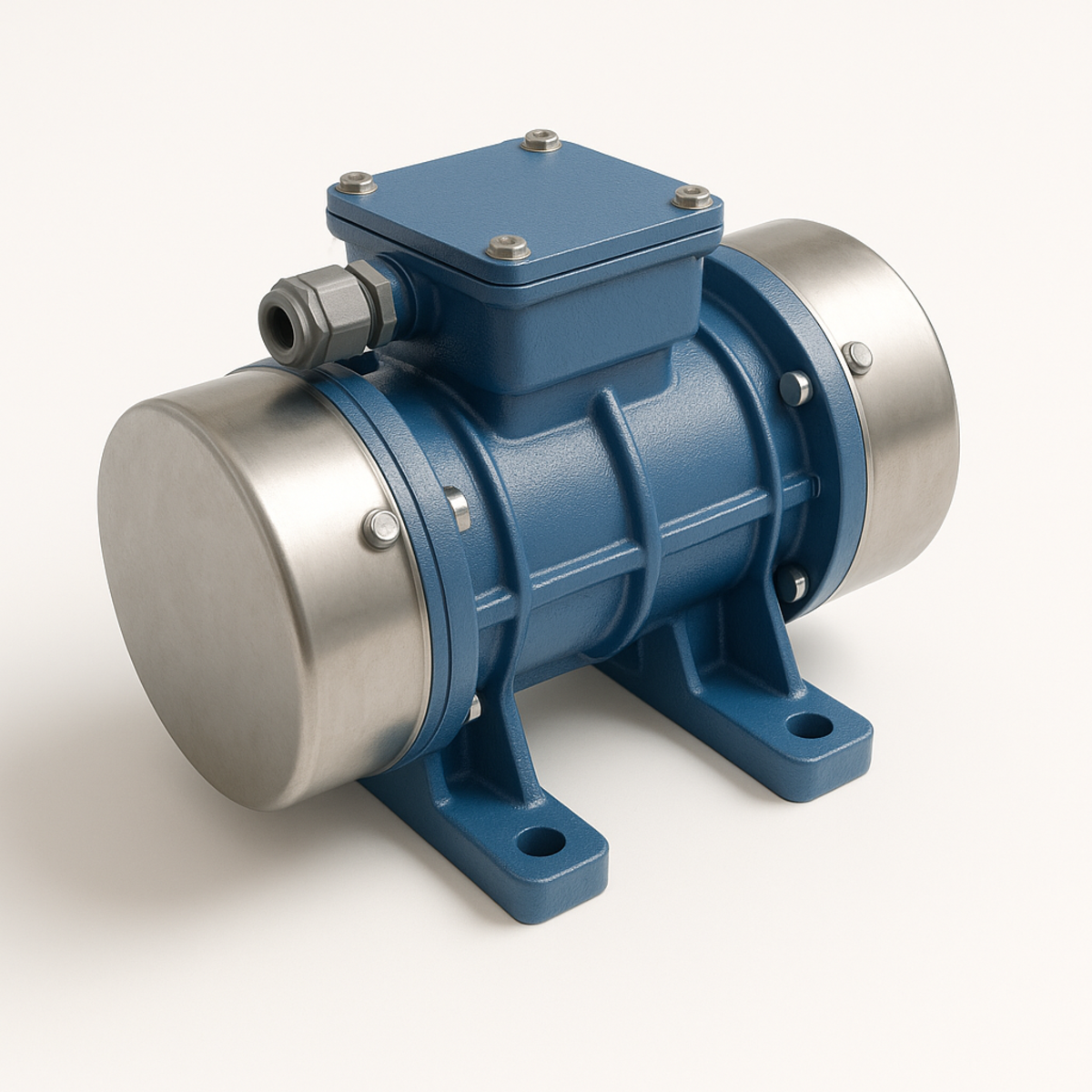
Pneumatische und hydraulische Lösungen
Wenn der Einsatz elektrischer Motoren nicht möglich oder nicht gewünscht ist – beispielsweise in explosionsgefährdeten Bereichen oder bei besonders aggressiven Umgebungsbedingungen – bieten pneumatische oder hydraulische Schwingungserzeuger eine bewährte Alternative. Sie nutzen Druckluft oder Flüssigkeitsdruck, um Kolben oder Membranen in Schwingung zu versetzen und dadurch mechanische Vibrationen zu erzeugen, die gezielt zur Förderung, Verdichtung oder Trennung von Materialien genutzt werden können.
Pneumatische Systeme zeichnen sich durch eine hohe Betriebssicherheit und einfache Wartung aus. Da sie ohne elektrische Energiequellen auskommen, sind sie ideal für den Einsatz in ATEX-Zonen oder unter extremen Umweltbedingungen geeignet.
Durch den Verzicht auf komplexe Elektronikkomponenten sind sie besonders robust und unempfindlich gegenüber Staub, Feuchtigkeit und Temperaturschwankungen.
Hydraulische Systeme kommen vor allem dort zum Einsatz, wo besonders hohe Kräfte oder exakte Steuerungsmöglichkeiten erforderlich sind. Durch den Einsatz von Hydraulikflüssigkeit können sehr gleichmäßige und kräftige Schwingungsbewegungen erzeugt werden.
Anwendungen der Schwingtechnik
Schwingtechnik in der Fördertechnik
Eines der häufigsten Einsatzgebiete der Schwingungstechnik ist die Fördertechnik. Hier sorgen Schwingförderer und Vibrationsrinnen für einen kontinuierlichen, gleichmäßigen Transport von Schüttgütern aller Art. Anders als bei klassischen Förderbändern gibt es bei schwingenden Systemen kaum bewegliche Teile, was den Verschleiß erheblich reduziert. Das senkt Wartungskosten und verlängert die Lebensdauer der Maschinen deutlich.
Dank der Kombination aus Motoren, Unwuchten und Steuerungstechnik kann der Materialfluss exakt angepasst werden. Selbst kleinkörnige, staubige oder schlecht rieselfähige Stoffe lassen sich damit effizient handhaben. Mit Hilfe von Schwingungsdämpfern wird verhindert, dass die erzeugten Vibrationen auf die Tragkonstruktion oder angrenzende Anlagenteile übergehen.
Schwingungen in der Prüf- und Messtechnik
In der Prüf- und Messtechnik werden Schwingungen genutzt, um reale Belastungen zu simulieren. Prüfstände erzeugen beispielsweise exakt dosierte Vibrationen, um die Haltbarkeit von Maschinenkomponenten, elektronischen Baugruppen oder ganzen Produkten zu testen. Ziel ist es, Schwachstellen frühzeitig zu erkennen und die Qualität zu sichern.
Gerade in der Automobil-, Luftfahrt- oder Verpackungsindustrie sind solche Prüfverfahren unverzichtbar. Schwingungsanalyse, Modalanalyse und Resonanzuntersuchungen liefern dabei wichtige Daten für die Entwicklung und Serienfertigung.
Einsatz in der Sieb- und Sortiertechnik
Auch bei der Trennung und Sortierung von Materialien spielt die Schwingtechnik eine tragende Rolle. In Vibrationssieben wird das zu verarbeitende Material in unterschiedliche Korngrößen getrennt – ein Verfahren, das sowohl in der Baustoff-, Recycling- als auch in der Lebensmittelindustrie eingesetzt wird. Durch gezielte Schwingbewegungen werden die Partikel bewegt, getrennt und außerdem noch gefiltert.
Die Siebfrequenz kann dabei so gewählt werden, dass das Siebergebnis optimal zur Anwendung passt. Besonders wichtig ist dabei, dass die eingesetzten Systeme robust gegenüber Staub, Feuchtigkeit und mechanischer Belastung sind – hier zeigt sich die Stärke der schwingtechnischen Bauweise.
Spezialanwendungen in der Medizintechnik, Lebensmittelindustrie u. a.
Auch in sensiblen Branchen kommt die Schwingtechnik erfolgreich zum Einsatz. In der Medizintechnik werden Vibrationen beispielsweise zur Entlüftung von Flüssigkeiten, zur Förderung empfindlicher Medikamente oder sogar in der Therapie genutzt.
Diese Anwendungen erfordern ein Höchstmaß an Hygiene, Präzision und Materialverträglichkeit. Daher kommen hier häufig elektromagnetisch betriebene Systeme oder speziell gedämpfte Schwingeinheiten zum Einsatz, die durch moderne Schwingungsdämpfer zusätzlich stabilisiert werden.
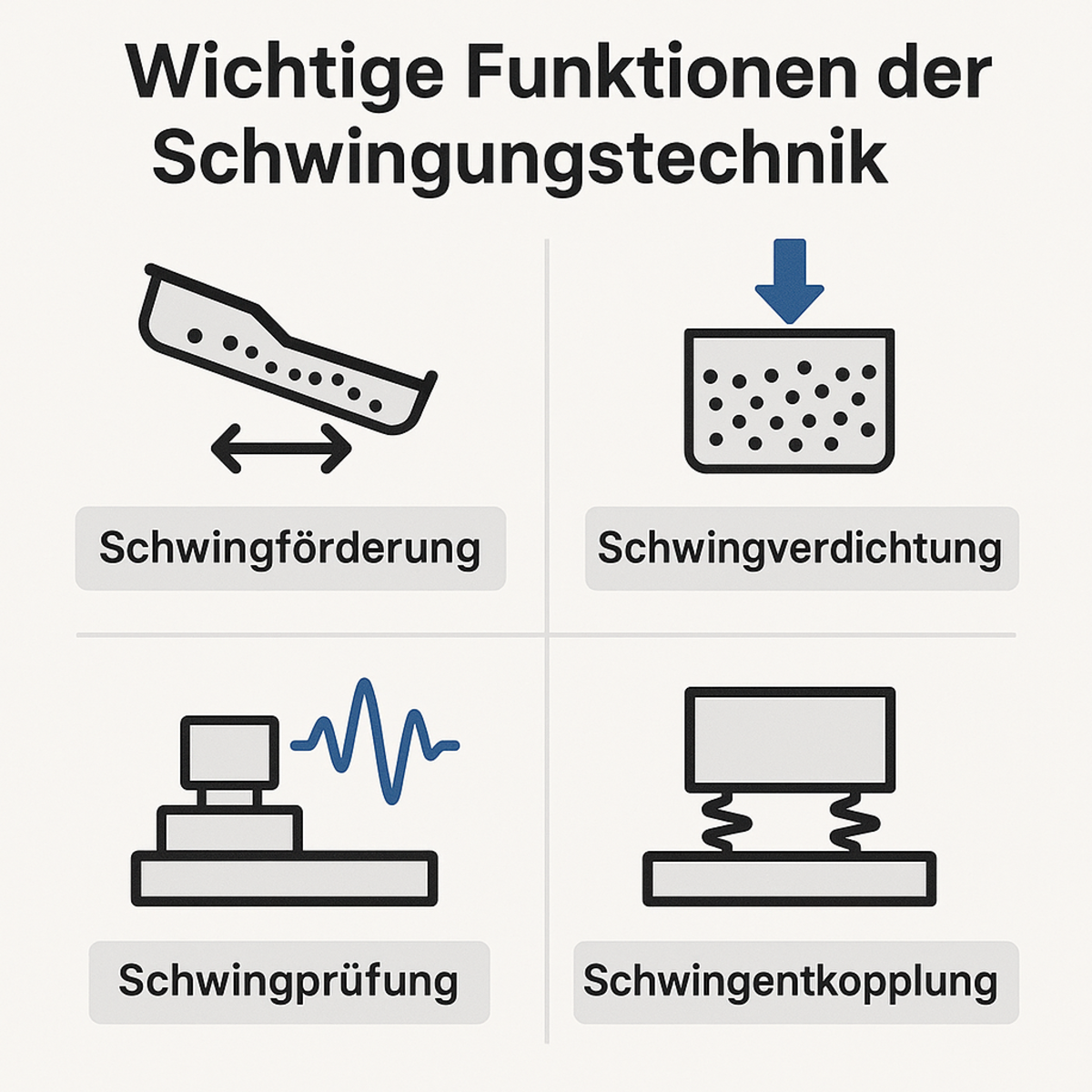
Komponenten und Systeme der Schwingtechnik
Die Schwingtechnik besteht aus einer Vielzahl spezialisierter Komponenten, die je nach Einsatzgebiet und Anwendungszweck individuell kombiniert und konfiguriert werden. Damit die erzeugten Vibrationen effizient und kontrolliert wirken, ist das Zusammenspiel von Antrieb, Trägerkonstruktion, Dämpfung und Steuerung entscheidend. Hochwertige schwingtechnische Systeme zeichnen sich durch präzise Abstimmung, Langlebigkeit und minimale Störanfälligkeit aus.
Schwingantriebe und Rüttler
Der Schwingantrieb ist das zentrale Element jeder schwingtechnischen Anlage. Er sorgt dafür, dass die gewünschte Bewegung – meist eine lineare oder oszillierende Schwingung – erzeugt wird. Dabei kommen je nach Anwendung unterschiedliche Technologien zum Einsatz: von einfachen Unwuchtmotoren über Magnetantriebe bis hin zu pneumatischen Rüttlern.
Rüttler sind in vielen Bereichen unverzichtbar – etwa zum Entleeren von Silos oder zur Verdichtung von Schüttgütern in Verpackungsprozessen. Sie erzeugen kraftvolle, gleichmäßige Schwingungen, die den Materialfluss fördern und Produktanhaftungen lösen. Durch die Verwendung robuster Motoren und widerstandsfähiger Materialien sind sie auch für den Dauerbetrieb in rauen Umgebungen bestens geeignet.
Schwingförderer und Vibrationsförderbänder
Schwingförderer transportieren Materialien ohne rotierende Elemente – nur durch die Kraft der Vibration. Das macht sie besonders verschleißarm, hygienisch und leise. Eingesetzt werden sie überall dort, wo empfindliche, abrasive oder schlecht fließende Materialien gefördert werden müssen – zum Beispiel in der Lebensmittel-, Pharma- oder Recyclingindustrie.
Vibrationsförderbänder nutzen eine Kombination aus Schwingtechnik und konventionellen Förderprinzipien. Sie lassen sich exakt auf das Fördergut und die gewünschte Taktung abstimmen und sind besonders für kontinuierliche Prozesse geeignet, bei denen konstanter Materialfluss entscheidend ist.
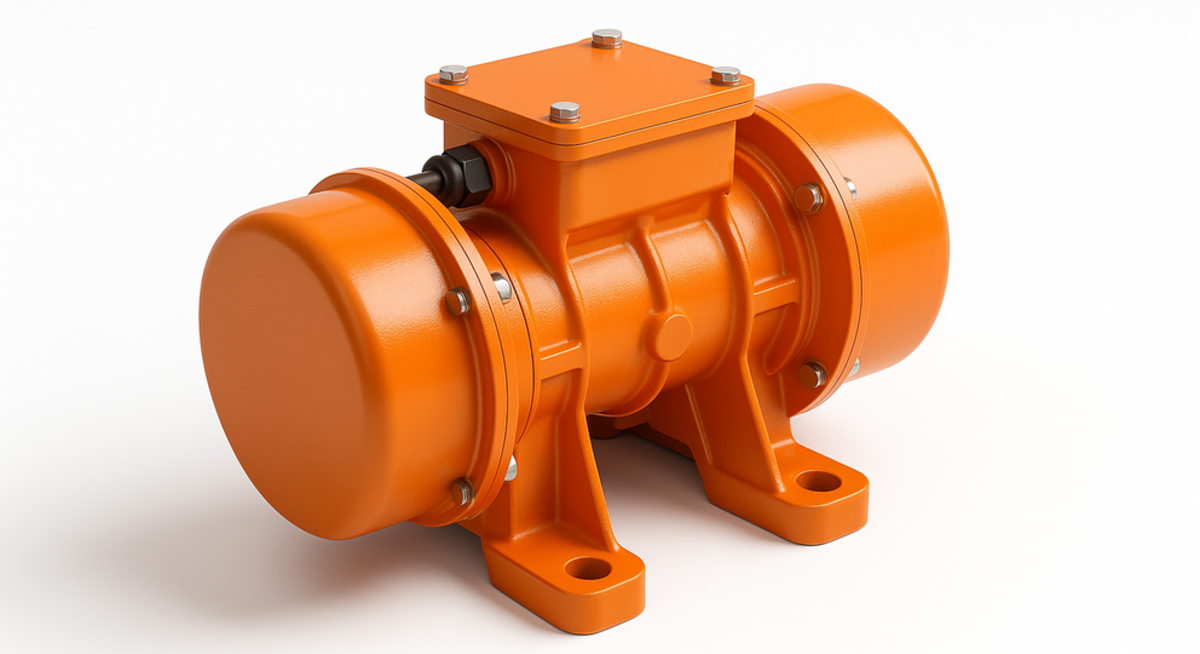
Schwingtische und -siebe
Schwingtische dienen dazu, Materialien durch kontrollierte Schwingungen zu verdichten, zu entlüften oder gezielt zu positionieren. Sie finden breite Anwendung in verschiedenen Industriezweigen – etwa beim Verpacken von Pulvern und Granulaten, bei der Verdichtung von Schüttgütern in Containern oder beim Betonverdichten im Bauwesen. Die Schwingbewegung sorgt dafür, dass Hohlräume im Materialgefüge geschlossen werden, wodurch eine höhere Dichte und bessere Stabilität erreicht wird.
Moderne Schwingtische verfügen über einstellbare Frequenzen und Amplituden, die es ermöglichen, die Vibrationsparameter optimal an das jeweilige Material und den Prozess anzupassen. Durch die flexible Steuerung können sowohl empfindliche als auch grobkörnige Materialien effizient verarbeitet werden.
Vibrationssiebe hingegen übernehmen die präzise Trennung von Feststoffen nach Korngröße oder Dichte. Dabei wird das zu siebende Material durch horizontale oder vertikale Schwingungen über das Siebdeck geführt. Die Bewegung bewirkt, dass kleinere Partikel durch die Sieböffnungen fallen, während größere zurückbleiben.
Steuer- und Regelungstechnik
Die Steuerung schwingtechnischer Systeme erfolgt heute meist über moderne Frequenzumrichter, Mikrocontroller oder SPS-Steuerungen. Dadurch lassen sich alle relevanten Parameter – wie Schwingfrequenz, Amplitude oder Taktzyklen – exakt steuern und überwachen.
Eine intelligente Regelung trägt dazu bei, dass Maschinen nicht nur effizient, sondern auch sicher arbeiten. Störungen im Materialfluss, ungewollte Resonanzen oder mechanische Überlastungen können frühzeitig erkannt und automatisch korrigiert werden. Darüber hinaus ermöglichen digitale Steuerungen die Integration in übergeordnete Automatisierungssysteme – ein entscheidender Vorteil für moderne Industrie-4.0-Umgebungen.
Schwingungsdämpfer spielen auch hier eine wichtige Rolle: Sie reduzieren die Übertragung von Vibrationen auf angrenzende Bauteile und gewährleisten so einen störungsfreien Betrieb, auch bei hoher Dynamik oder empfindlichen Umgebungen.
FAQ zu Schwingtechnik
Die Schwingungstechnik erzeugt gezielt Vibrationen zur Prozessoptimierung, während Vibrationsisolierung unerwünschte Schwingungen mithilfe von Schwingungsdämpfern reduziert oder entkoppelt. Beide gehören zur Schwingtechnink, verfolgen aber unterschiedliche Ziele.
Schwingungsdämpfer wandeln Schwingungsenergie in Wärme um oder entkoppeln Bauteile durch elastische Materialien. Sie schützen Maschinen und Motoren vor schädlicher Vibration und verlängern die Lebensdauer technischer Komponenten.
Schwingungstechnik findet sich in Förderanlagen, Siebmaschinen, Rütteltischen, Prüfständen und Vibrationsmesssystemen. Besonders in Maschinen mit rotierenden oder schlagenden Bewegungen helfen Schwingungsdämpfer, Vibrationen zu kontrollieren.
Die Frequenz bestimmt, wie oft eine Schwingung pro Sekunde auftritt. Sie beeinflusst maßgeblich die Intensität und Wirkung der Vibration. Eine falsche Frequenz kann Resonanz erzeugen und Maschinen beschädigen.
Vibrationen in Motoren lassen sich durch Auswuchten, elastische Lagerungen, regelmäßige Wartung und den Einsatz geeigneter Schwingungsdämpfer minimieren. Ziel ist ein ruhiger, langlebiger Betrieb.
Entscheidend sind Fördergut, Einbausituation, Frequenzbereich und Antriebsart. Der Rüttler muss zur Maschine, zur Umgebung und zur gewünschten Schwingungstechnik passen – auch in Bezug auf Energieeffizienz und Steuerung.
Wichtige Normen sind DIN ISO 10816 für Maschinenschwingungen und die Maschinenrichtlinie 2006/42/EG. Sie regeln Sicherheit, Dämpfungsverhalten und zulässige Schwingungspegel für verschiedene Anlagen.
Sensoren erfassen Vibrationen an Maschinen oder Motoren, die per Software ausgewertet werden. So lassen sich Unwuchten, Schäden oder Resonanzverhalten erkennen – ideal für vorausschauende Wartung.
Geeignet sind schwingfeste Stähle, Aluminiumlegierungen, Verbundwerkstoffe und Elastomere. Sie halten mechanischer Belastung stand und unterstützen die Funktion von Schwingungsdämpfern.
Zu den Trends zählen digital gesteuerte Schwingsysteme, adaptive Dämpfer, energieeffiziente Antriebe und smarte Sensorik. Auch nachhaltige Materialien gewinnen in der Schwingungstechnik an Bedeutung.